Blog
What is a Post-Processor?
A Post-Processor serves as a crucial software intermediary, translating the outputs from Computer-Aided Manufacturing (CAM) systems such as CATIA, 3DExperience, Siemens NX, Mastercam into machine-specific code compatible with your CNC (Computer Numerical Control) machine. It functions as the essential link between your CAM system and the machine tool on your shop floor. While you programming a tool path for a part in your CAM system, you’re essentially using a distinct coding language. The post-processor steps in, taking this language and transforming it into G-code, which is then executed by the machine tool.
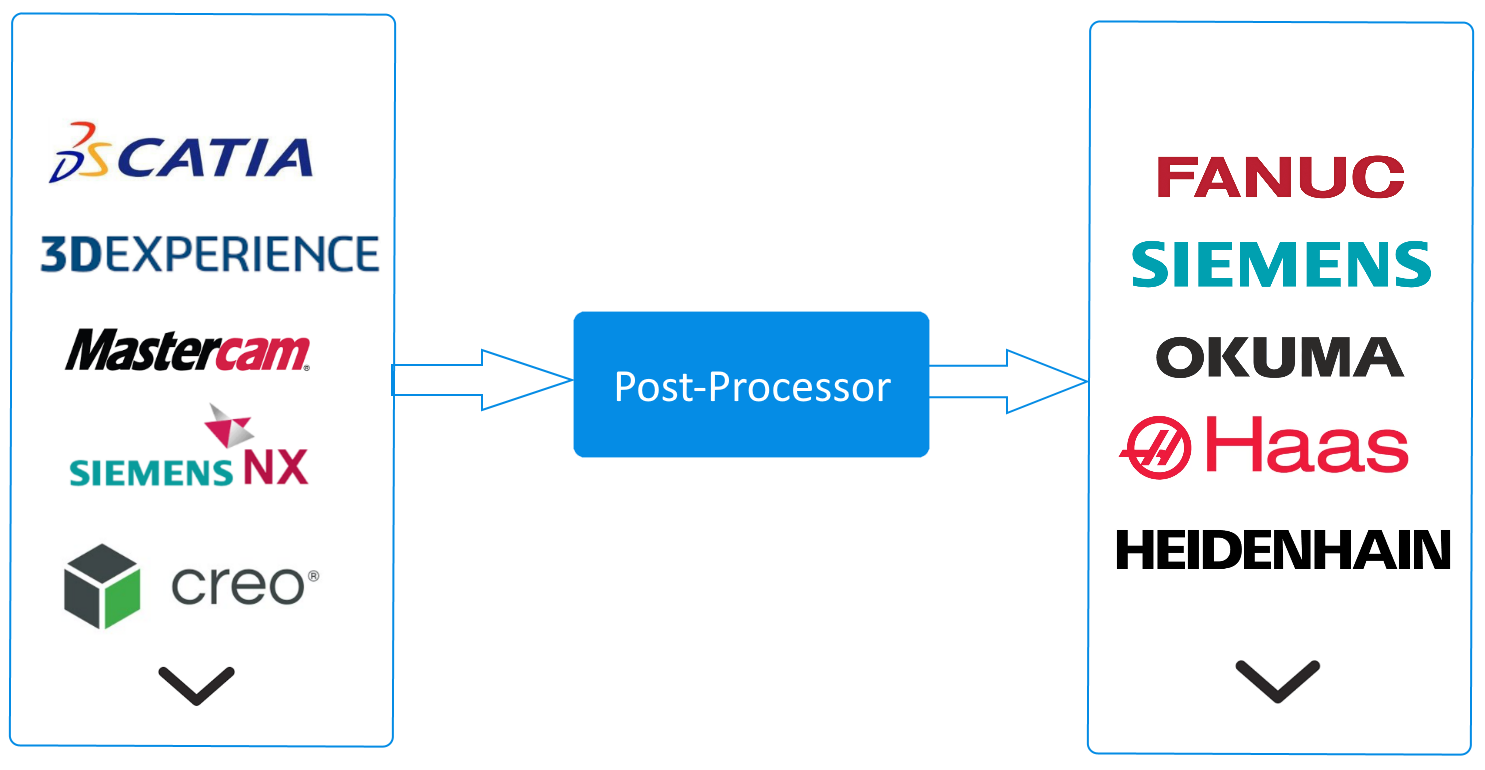
Having a high-quality post processor is pivotal in your manufacturing workflow as it ensures a seamless transition from your CAM-created design to the precise execution on the machine, ultimately producing a quality part. The type of post processor you require is contingent upon the specific machine tool you use, and their complexity can vary. Each post processor demands configuration tailored to the Original Equipment Manufacturer (OEM) machine tool, its specific model, and any specialized features it may incorporate.
Whether you’re working with a straightforward 3-axis mill or a more sophisticated machine employing rotary axes, the post processor plays a critical role. For advanced machines with rotary axes, the post processor needs to comprehend how to manipulate these axes, ensuring the tool remains in contact with the part while adhering to machine limitations. In essence, a well-configured post processor is the linchpin in your manufacturing process, translating your design intentions into precise machine instructions.